How to Efficiently use Warehouse Management to Reduce Costs
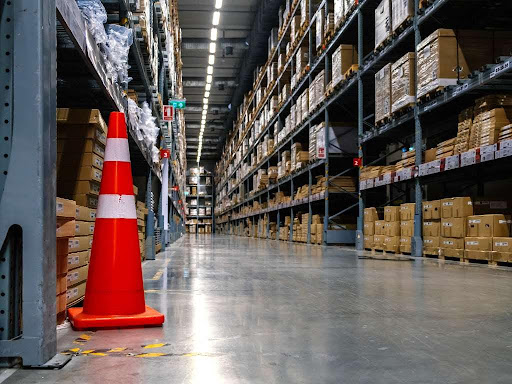
An efficient warehouse is a facility that allows you to reduce merchandise handling costs, increase productivity, and offer the highest quality of service to customers. Considering the importance of a warehouse for any company’s activity, we have prepared this list of tips for achieving an efficient warehouse and, consequently, an adequate organization of operations and available resources.
1. Optimize the warehouse layout
Optimizing warehouse layout is an effective way to both maximize space and facilitate operations within any logistics facility. An effective warehouse should feature storage systems that maximize productivity while taking advantage of any available space, whether through manual (operators insert and extract goods from their locations) or automatic solutions (handling equipment manages goods autonomously).
2. Flag the warehouse
Warehouse signage is a preventive measure designed to minimize risks for logistics professionals. Efficient warehouses use colors, pictograms, light panels, and acoustic signals to help operators identify restricted access areas or forklift circulation areas. Signage’s priority is to ensure the safety of operators and goods while improving efficiency. In a properly signed warehouse, operators’ movements and actions are limited to avoid possible accidents and achieve maximum productivity in each operation.
3. Label the products
Merchandise coding is a fundamental process for achieving efficiency in a warehouse. Products must be properly labeled with a barcode , QR code or RFID tag to simplify their identification and subsequent location . Product coding allows the company to quickly check the characteristics of each item, such as its reference, date of arrival at the warehouse, packaging, ingredients or hazardousness. Correct merchandise coding allows for more rigorous monitoring of product traceability and, consequently, streamlines warehouse operations.
4. Classify inventory according to its turnover (ABC method)
Good merchandise organization has a positive impact on the different operations that take place in the warehouse. Classifying merchandise according to the ABC method allows products to be distributed based on their relevance to the company, value, and turnover.
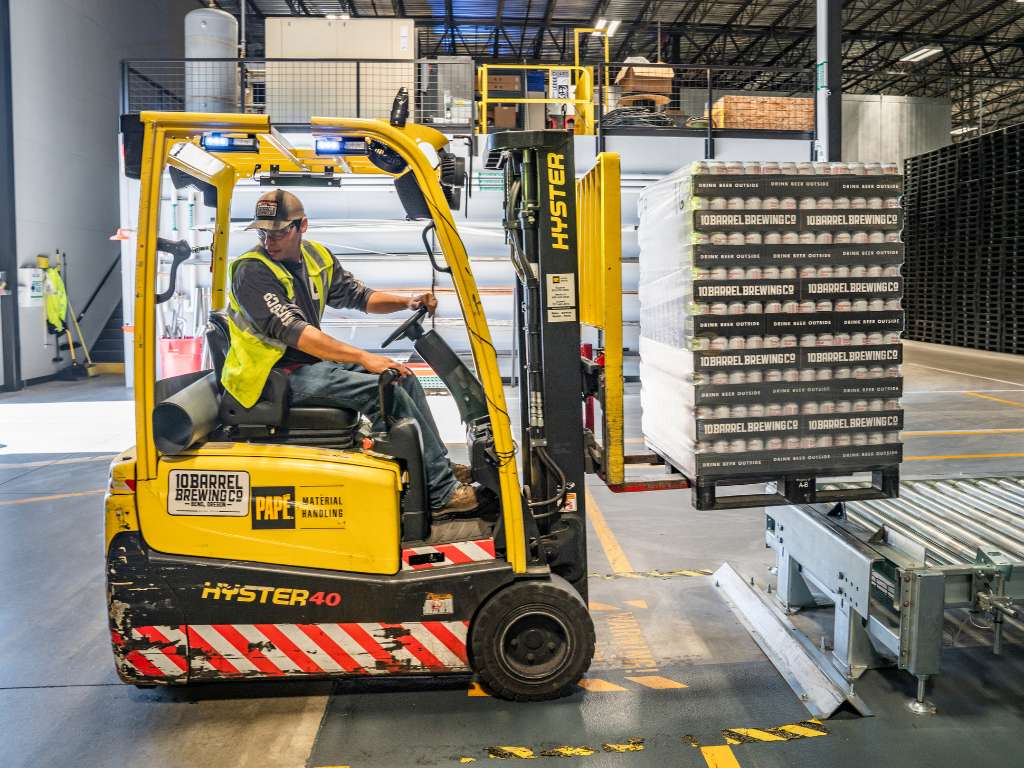
5. Define the criteria for preparing orders
In an efficient warehouse, it is essential to implement a method that favors the preparation of the greatest possible number of orders . This will depend on the number of daily orders, the items’ dimensions and characteristics, and the warehouse’s size. What are the most common order preparation methods? The “person-to-product” method involves operators walking around the warehouse to the locations to pick the products that make up each order; and the “product-to-person” method eliminates operator movement and, as a result, provides excellent performance.
6. Cross-dock when possible
A warehouse can achieve greater efficiency by eliminating unnecessary operations. One way to achieve this is through cross-docking , a technique in which goods arrive at the warehouse and are dispatched almost immediately. Therefore, storage is very short or can even be eliminated.
7. Digitize warehouse management
Digitizing your warehouse is the first step towards increasing logistics and distributing company Dubai efficiency. An essential tool is warehouse management software (e.g. Easy WMS by Mecalux) . This program acts as the brain of the facility, coordinating all processes and guiding operators in each assigned task. Implementing this software eliminates the risk of errors in stock movement, product extraction and location, and order preparation. It also speeds up operations by reducing distances traveled and automating decision-making. In addition, the system can increase the warehouse’s capacity thanks to intelligent space management.
8. Plan inventory
Stock is the main asset of any company, so it is essential to manage it correctly . Stock shortages , caused by a lack of foresight, cause orders to be delivered to customers late. On the other hand, excess stock can occur , such as an excess of merchandise in the warehouse, which increases costs and the risk of deterioration of the items. How can you plan stock in an efficient warehouse? With the help of technology. For example, warehouse management software can accurately monitor products and organize supply tasks based on the company’s needs and the number of orders that must be completed.
9. Control inventory in real time
Controlling stock in real time is essential for companies that manage a wide range of references or have different logistics facilities and points of sale. Implementing stock software , such as a Warehouse Management System, allows you to permanently control stock: every movement made by a product ─ from its receipt to its dispatch ─ is recorded in the software thanks to radio frequency terminals . In this way, the logistics manager has full visibility of the stock, obtaining complete traceability of the goods and avoiding stock losses.
10. Reduce warehouse movements
In an efficient warehouse, the movement of operators and products is reduced to a minimum. For example, the facility can be divided into work areas, each assigned to a specific number of operators. This way, each operator works in the assigned area without traveling through the entire warehouse to locate the products. Management software lets you map the most appropriate picking and stock movement routes .
11. Simplify shipping
The dispatch of goods is a fundamental phase in ensuring good logistics services. Planning shipments, classifying orders and generating the necessary documentation in advance are processes that must be optimized to have an efficient warehouse. Implementing a specific program for this phase (such as Mecalux’s logistics dispatch management software ) facilitates an agile and efficient dispatch process . This type of program is integrated with the software of the main transport agencies to generate labels for carriers and delivery notes for each outbound order without errors.
12. Introduce picking assistance systems
Order picking is one of the most demanding freight forwarder processes in a warehouse. To increase productivity in this operation, there are assistive devices that guide operators at all times and reduce the risk of errors. How? Pick-to-light or voice-picking devices connect to management software to transmit instructions to the operator ─ for example, the items and the quantity to be extracted from each location ─ and help them complete the largest number of orders in the shortest possible time.
13. Organize warehouse locations
Distributing goods in a warehouse is a complex process that can generate excessive costs when managed manually. Organizing goods manually can result in a real space waste and increase operator routes’ complexity. Management software can organize warehouse locations in warehouses with many SKUs more efficiently. For example, Mecalux’s EasyWMS has slotting software that analyzes product demand and turnover to automatically assign the appropriate location to each SKU.
14. Synchronize warehouse inventory with online and physical stores
The omnichannel strategy has increased the complexity of logistics, as it has forced companies to synchronize inventory across their numerous points of sale (both online and physical stores). Any mismatch between the inventory in the warehouse and that displayed on the website or marketplace can delay the delivery of an order. To address the challenges of the omnichannel strategy, companies are using digital solutions. For example, Mecalux’s Marketplaces & Ecommerce Platforms Integration and Store Fulfillment programs synchronize warehouse inventory with the catalog of items in online stores and physical stores. This makes optimizing inventory supply between the central warehouse and the different physical stores possible.
15. Increase warehouse capacity
It is essential to make the most of storage capacity to increase efficiency. Numerous solutions allow you to add storage space without having to purchase more floor space: in the case of picking warehouses, platforms can be installed , which multiply the installation levels, or live picking racks , which increase depth and simplify order preparation. Some solutions increase capacity in pallet warehouses, such as mobile racks , drive-in racks and the Pallet Shuttle system.